【研究背景】
为提高资源利用效率、降低化石燃料消耗、提高热效率,并改善构件使用寿命,高温结构零件用材料亟需开发更稳定可靠使用的合金。而高温工程用材料的关键结构-性能关系由其微观组织和沉淀相形态决定。为此,提升微观结构稳定性可用于开发新材料和发展新的强化理念。常用的高温环境材料有钢(Fe基)和镍基高温合金,它们出色的抗粗化和抗蠕变性能源于其双相微观组织结构,即有序的沉淀相嵌入在无序的基体相中。然而,高温合金的设计空间逐渐狭窄,尤其是对于镍基高温合金,发展新的概念和方法成为改进这些材料的必要之举。
最近,研究人员提出的在主沉淀相内形成纳米级颗粒的分层微结构,可以提高Fe基和Ni基合金的蠕变抗性和机械性能。如在Fe基合金中:
• α(A2基体相)⊃ α1(D03沉淀相)⊃ α(A2颗粒),
• α(A2基体相)⊃ τ1(L21 Heusler相沉淀)⊃ β(B2颗粒)。
在Ni基、Co基和高熵合金中的分层微结构为:
• γ(A1基体相)⊃ γ'(L12沉淀相)⊃ γ(A1颗粒)。
随着高分辨率表征技术的兴起,如透射电子显微镜(TEM)和三维原子探针技术(APT),为人们解析这些纳米颗粒的结构和组成提供了可能性。然而,要充分利用分层微结构的强化效应,必须解决其在高温下的亚稳定性问题。这些颗粒要么继续生长并分离主沉淀相,要么随着时间的推移在主沉淀相内溶解,使得热机械强度降低。因此,如何控制和调整纳米颗粒的形态、大小和体积分数以提高热稳定性是一个关键问题。
【文章简介】
近日,来自海南大学精密仪器高等研究中心的Florian Vogel 研究员,在国际知名期刊Journal of Alloys and Compounds上发表题为“Tracking maze-like hierarchical phase separation behavior in a Fe-Si-V alloy”的研究论文。
为了优化下一代高温和耐腐蚀合金的性能,作者综合运用透射电子显微镜(TEM)和三维原子探针技术(APT)这两种方法,通过研究单晶Fe79.5Si15.5V5.0(at.%)高温合金的分层微结构相分离行为,深入探讨了高温合金结构-性能关系和相化学平衡的关键机制。研究揭示了Fe79.5Si15.5V5.0的一个错综复杂的迷宫状分层微结构:在有序α1(D03)沉淀相内部形成了迷宫状的亚稳定的无序α板状纳米颗粒(A2相)。通过对晶体结构、晶格失配和弹性应变的分析,作者深入研究了α(A2)板状纳米颗粒的形态。通过对相组成和三元相图的热力学评估,解析了分层微结构相分离机制的混合吉布斯能。通过与其他合金体系的具有分层微结构比较,提出了改进分层微结构稳定性的策略。此外,作者还发现了弹性各向异性比(Zener比)是预测层次颗粒形态的关键指标,这一发现为理解分层微结构的稳定性提供了新的视角,将对未来合金设计和优化提供有益的指导。最终,作者提出通过考虑不同相中各元素的分配行为,以生成纳米颗粒相为目标,可进行针对性合金设计,改善纳米颗粒相的热稳定性,从而实现对分层微结构的强化效应。这项研究为改进高温结构材料性能提供了潜在途径,并不仅限于Fe79.5Si15.5V5.0的合金体系。
【本文要点】
要点一:Fe-Si-V合金在高温下发生了相分离,形成了迷宫状的分层微结构
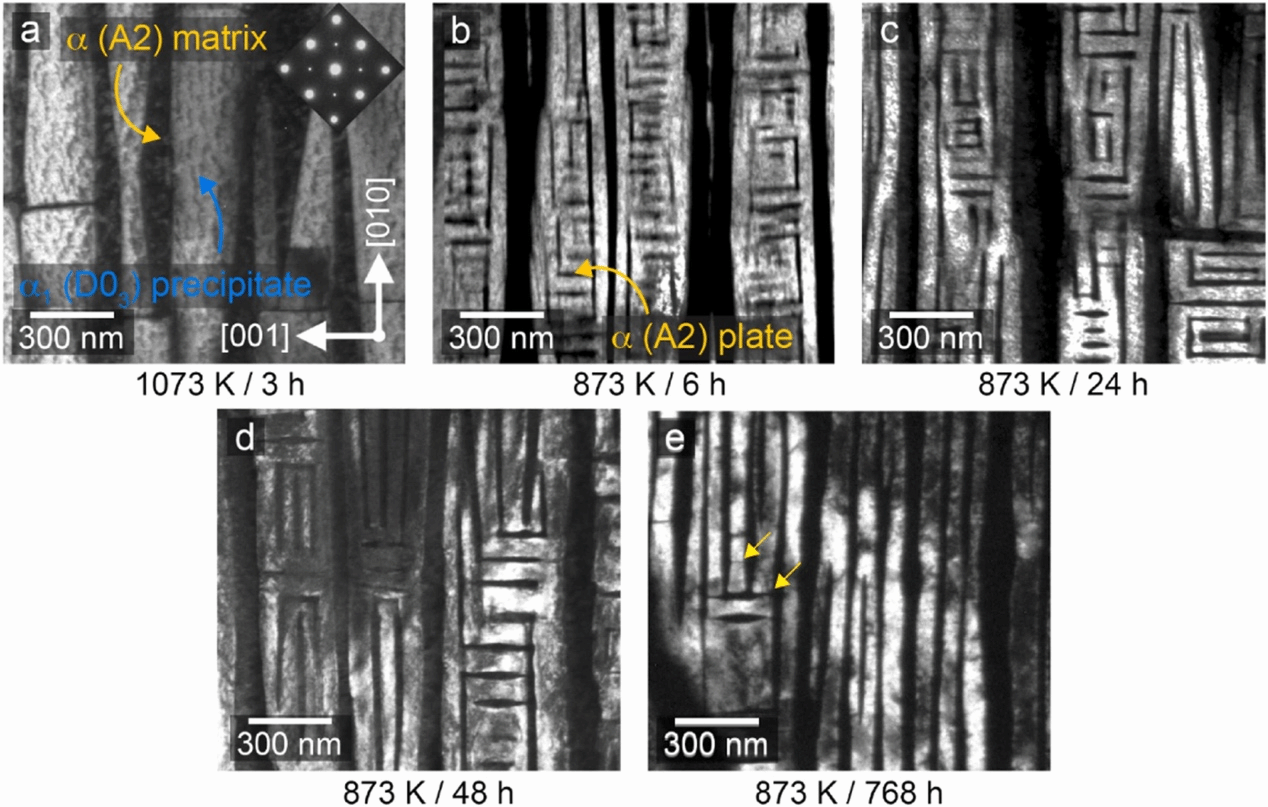
图1. 在不同时效阶段的Fe79.5Si15.5V5.0模型合金的DF-TEM图像。 (a) 1373 K/6小时均质化处理和1073 K/3小时时效后的两相微结构。插图中的SAED图像显示观察取向为[001],以及α (A2)基体中α1 (D03) 沉淀相的超晶格衍射斑点。 (b) 在随后的873 K/6小时时效中,分层相分离形成了一个“迷宫状”图案,其中α1 (D03)沉淀相内部出现α (A2)板状纳米颗粒。 (c) 873 K/24小时时效,α (A2) 板状纳米颗的粗化。 (d) 在873 K/48小时时效后,α (A2) 相沿[010]方向形成了细长的板状纳米颗粒。 (e) 在873 K/768小时时效后,α (A2) 板状纳米颗与α (A2)基体融合并分离α1 (D03)沉淀相(用黄色箭头标记)。
作者发现,Fe-Si-V合金在1073 K时效3小时后,由于Fe和V的扩散,形成了有序的α1(D03)沉淀相和无序的α相(A2),α1(D03)沉淀相为板状或杆状,分布在α相(A2)的基体中。而在870 K 时效6小时后,在 α1 (D03)沉淀相中进一步析出了板状的无序α(A2)纳米颗粒,形成了迷宫状的分层微结构。并且α(A2)板状纳米颗粒是亚稳的,随着时效时间延长继续生长,直到它们分离α1(D03)沉淀相并与α(A2)基体相合并。
要点二:揭示了在不同状态下形成的α(A2)纳米颗粒和α1(D03)沉淀相之间的复杂演变和三维纳米化学
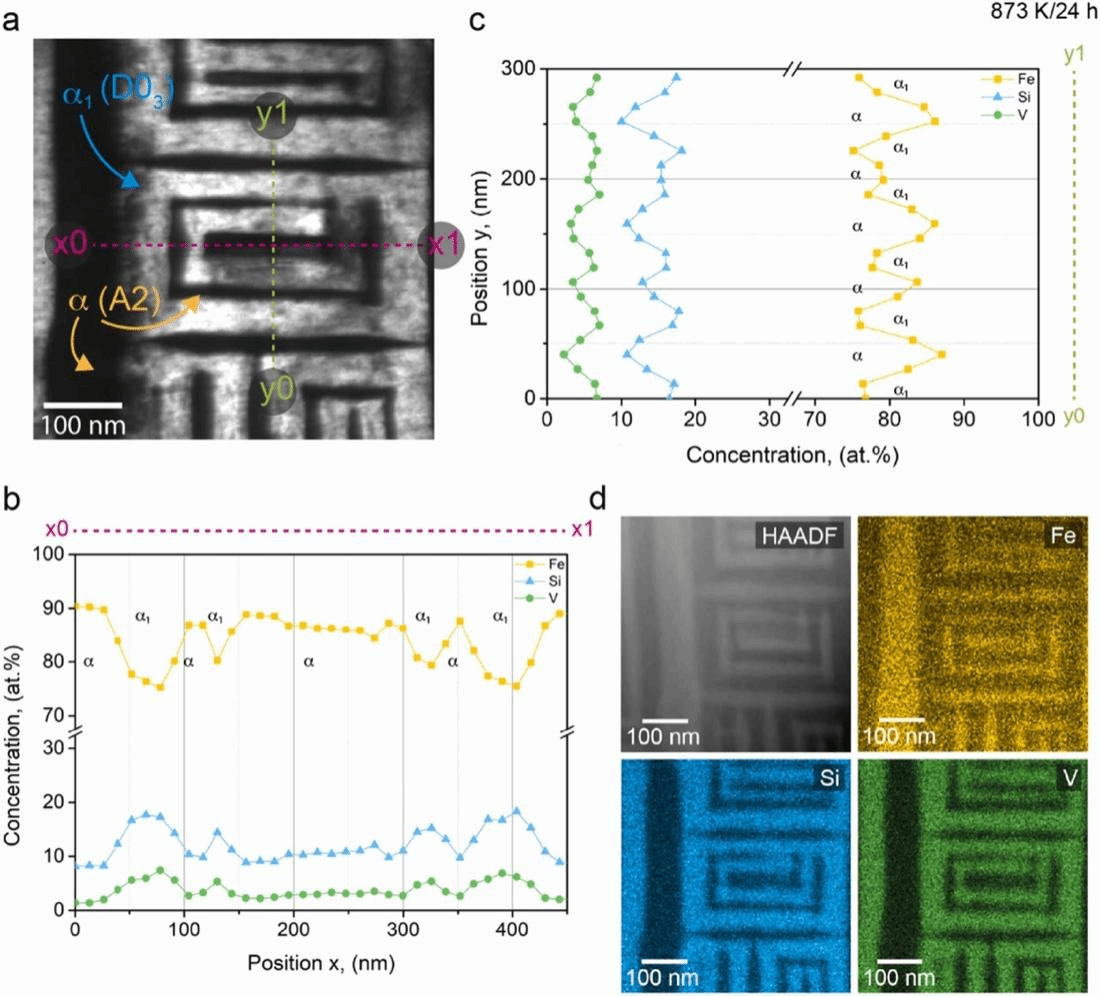
图2. 1073 K/3小时时效后,Fe79.5Si15.5V5.0模型合金的分层微结构经过随后的873 K/24小时时效的TEM-EDS分析。 (a) DF-TEM图像包括α (A2)基体(暗色),嵌入α1 (D03)沉淀相(亮色)的α (A2)板状纳米颗粒(暗色)。沿着虚线x0-x1(品红色)和y0-y1(绿色)获取EDS线扫描。 (b) 沿着x0-x1 和 (c)沿着y0-y1的Fe,Si)和V的浓度剖面,突显了α (A2)和α1 (D03)相的变化。 (d) HAADF-STEM图像和TEM-EDS元素mapping图,与 (a) 中区域一致,显示了Fe,Si和V的分布。
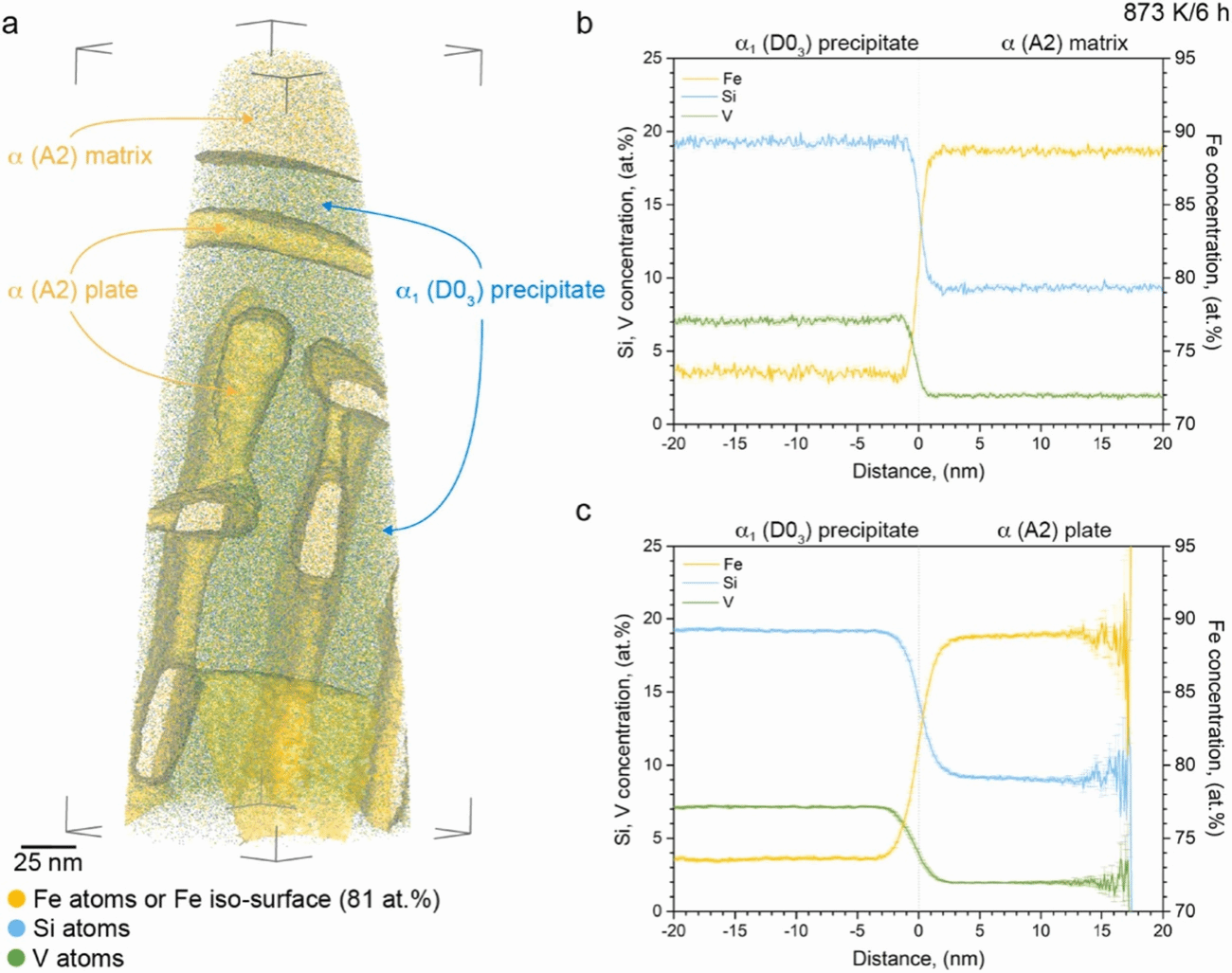
图3. 均质化后,Fe79.5Si15.5V5.0模型合金在1073 K/3小时时效和随后的873 K/6小时时效后的APT分析。 (a) APT数据集的3D重建,仅显示了部分Fe,Si和V原子以增强展示效果。通过81 at% Fe等面可视化α (A2)和α1 (D03) 相之间的界面。 (b) α1 (D03)沉淀相和α (A2) 基体之间界面的近邻图。 (c) α1 (D03)沉淀相和α (A2) 板状纳米颗粒之间界面的近邻图。
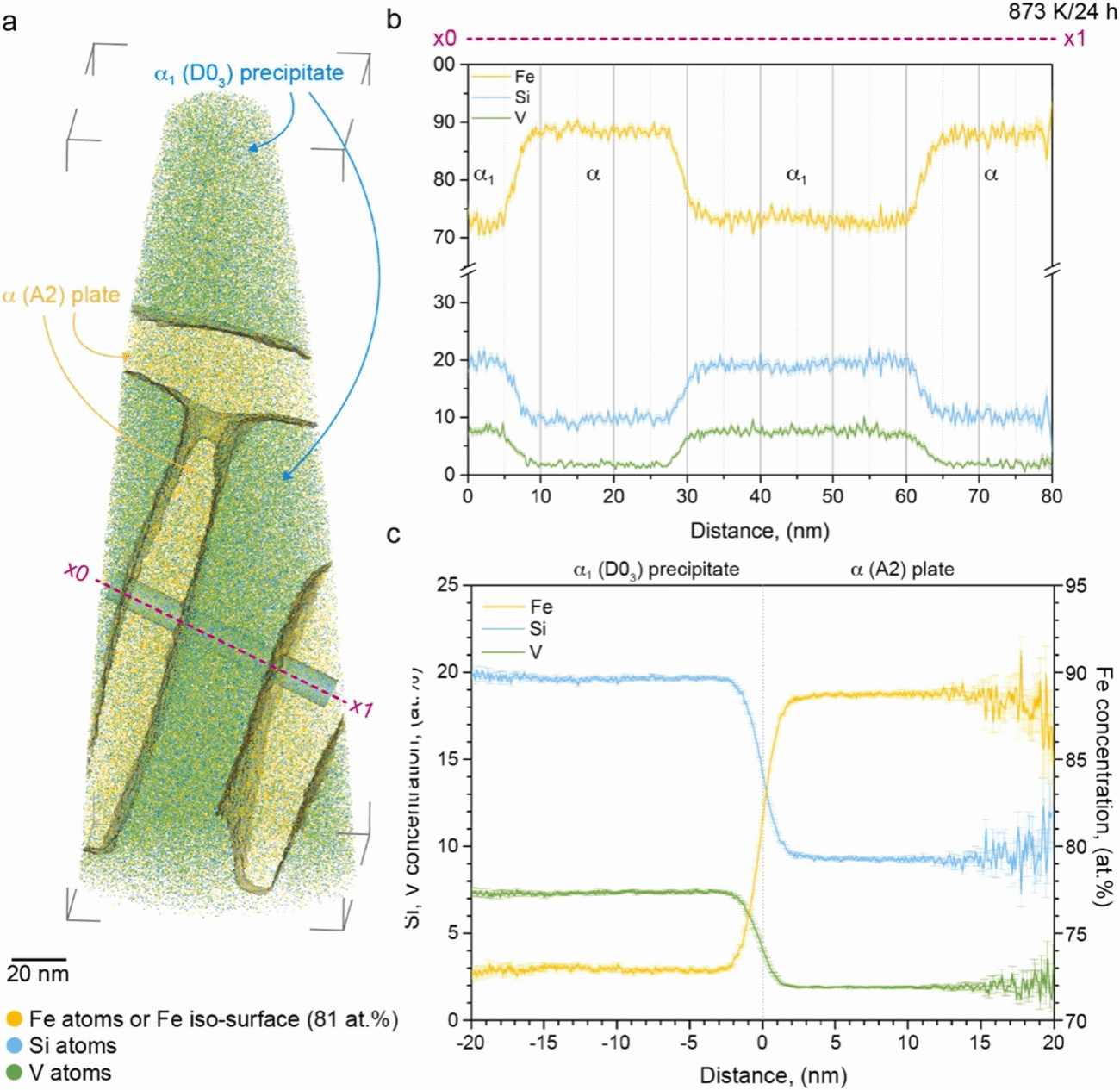
图4. 均质化后,Fe79.5Si15.5V5.0模型合金在1073 K/3小时时效和随后的873 K/24小时时效后的APT分析。 (a) APT数据集的3D重建,仅显示了Fe、Si、V的部分原子以增强展示效果。通过81 at% Fe等面可视化α1 (D03) 沉淀相和α (A2) 板状纳米颗粒之间的界面。 (b) Fe、Si和V的浓度分布图,清晰地显示了沿着(a)中的x0-x1(品红色)虚线获取的交替相。 (c) α1 (D03) 沉淀相和α (A2) 板状纳米颗粒之间的界面的近邻图。误差为标准偏差σ。
作者详细分析了Fe79.5Si15.5V5.0模型合金在不同时效状态下的分层微结构的化学成分,发现Fe会优先分配在α(A2)基体相和α(A2)纳米颗粒中,而Si和V在α1(D03)沉淀相中呈现出优先分配的趋势。
要点三:分层微结构中各相的尺寸、形态和体积分数随时效时间和温度变化而演变
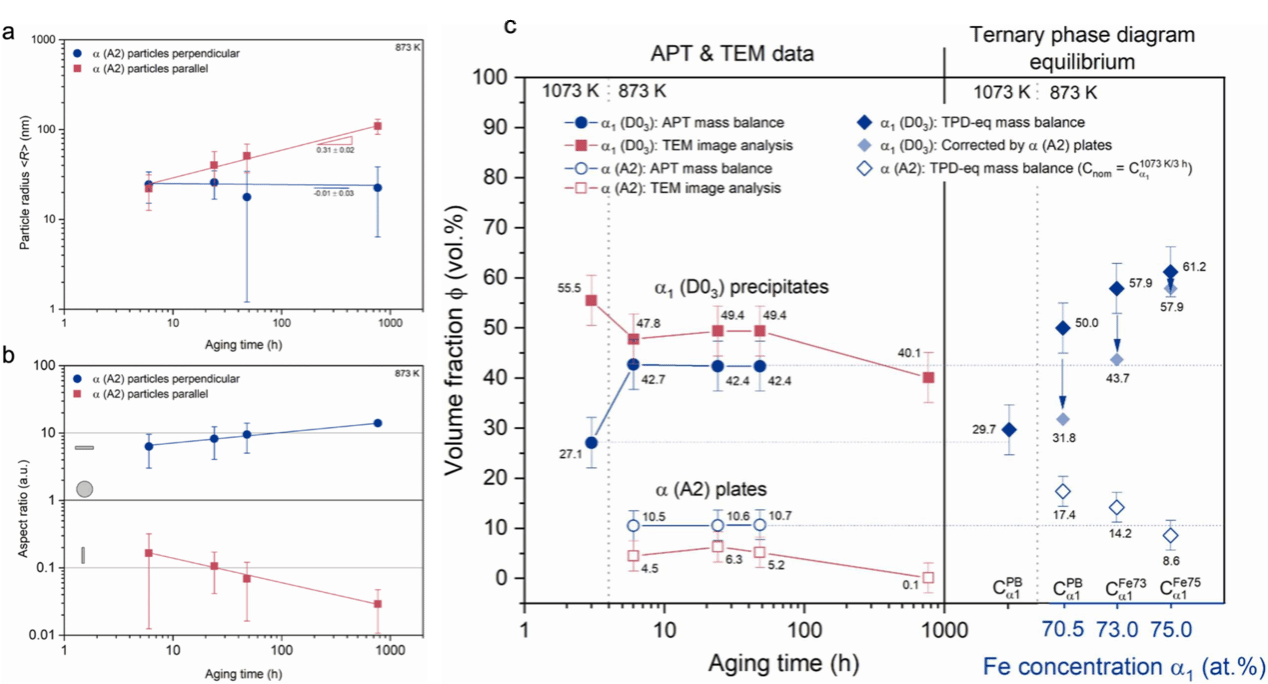
图5. Fe79.5Si15.5V5.0模型合金在1073 K时效3小时,随后873 K时效6小时、24小时、48小时和768小时的微结构尺寸与体积分数的演变。(a)垂直(蓝色圆圈)和平行(红色方块)α (A2) 板状纳米颗粒的平均等效半径 <R>。实线(蓝色和红色)表示与 <R> ∝ tn 关系的线性拟合,其中斜率 n 表示生长速率。(b) 垂直方向(蓝色圆圈)和平行方向(红色方块)α (A2) 板状纳米颗粒的长宽比(实线表示线性拟合)。(c) α1 (DO3)沉淀相体积分数φα1(实心符号)和α (A2) 板状纳米颗粒体积分数φα(空心符号)的演变。误差为标准偏差σ,根据标准误差传播方法计算。
作者对α(A2)板状纳米颗粒的生长和粗化进行了定量分析。指出了α(A2)板状纳米颗粒存在方向依赖性生长,观察到在垂直和平行方向上的不同行为。垂直α(A2)板状纳米颗粒的平均等效半径 <R> 保持不变,而平行α(A2)板状纳米颗粒的 <R> 随时间增长。作者还比较了α1(D03)沉淀相和α(A2)板状纳米颗粒的体积分数,并讨论了它们在时效过程中的变化。在时效873 K的前648小时内,α1(D03)沉淀相的体积分数达到平衡,之后基本保持恒定,然而在时效768小时后,观察到α1(D03)沉淀相的体积分数出现进一步的减小;通过TEM和APT数据分析,发现α(A2)板状纳米颗粒的体积分数在时效873 K的前648小时内保持不变,TEM数据显示在时效768小时后略微减小,而通过APT数据测得的体积分数相对较高,说明TEM测得的3D迷宫状结构的体积分数偏低。α(A2)板状纳米颗粒的体积分数随着时效的进行,其数量减少,因为它们生长并开始合并,最终如果长度足够,则平行排列的α(A2)板状纳米颗粒将转变成α(A2)基体通道。这说明α(A2)板状纳米颗粒的存在会延缓α1(D03)沉淀相的变化。
要点四:α1(D03)沉淀相中的Fe和V的过饱和导致α(A2)板状纳米颗粒的形成,从而降低了混合焓
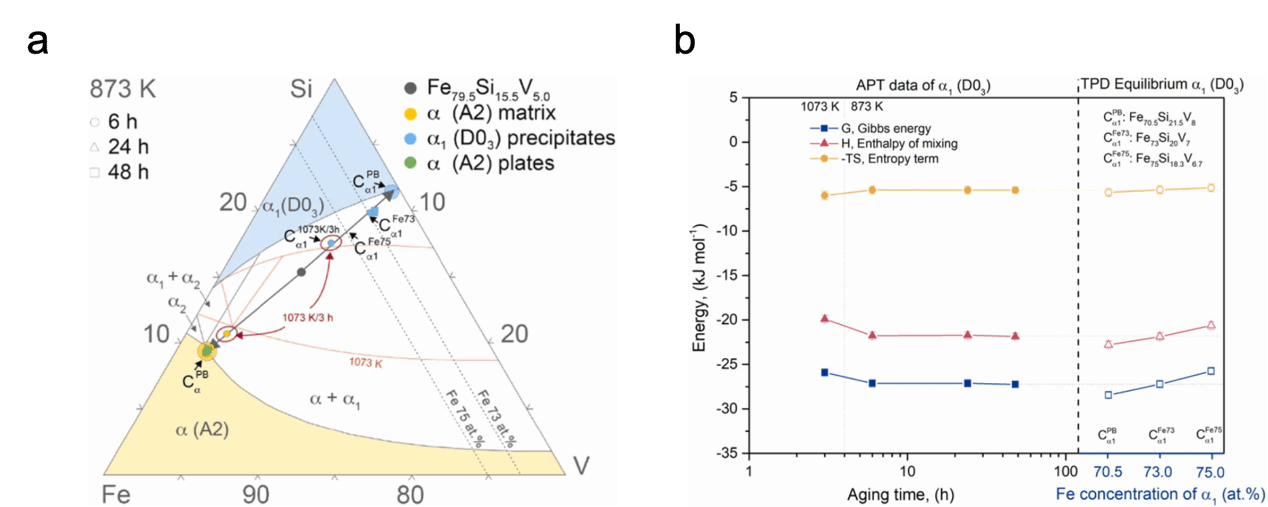
图6. (a)Fe-Si-V三元相图在873 K时的等温截面。(b)在1073 K时Fe-Si-V合金时效3小时,随后在873 K时效6小时、24小时和48小时期间的混合吉布斯自由能Gmix、混合焓Hmix和熵-TS。
作者指出,在1073 K 时效过程中,α1(D03)沉淀相中的Fe和V的平衡浓度较高,当温度降至873 K 时,Fe和V的过饱和使得α1(D03)沉淀相的自由能增加,从而促进了α(A2)板状纳米颗粒的析出。α(A2)板状纳米颗粒的析出使得α1相(D03)中的Fe和V含量降低,从而降低了α1(D03)沉淀相的自由能,使得系统的总自由能降低。
要点五:α1(D03)沉淀相的Zener比率ar(弹性各向异性比率)是α(A2)纳米颗粒形态的控制因素,可用于预测它们的形态演变
表1. 具有无序基体/有序沉淀物的合金的物理和弹性性能。
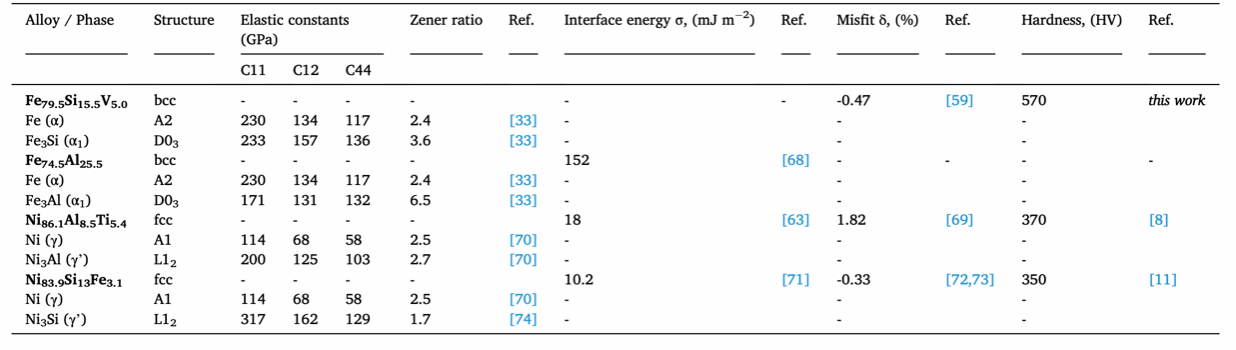
作者指出,在α(A2)板状纳米颗粒不断长大的过程中,即形态由球形变为板状或棒状,Zener比在α(A2)纳米颗粒(B)形态变化中起着关键作用。当主沉淀相(A)的Zener比(arB)较低时,层状颗粒在时效过程中仍然保持球形。当主沉淀相的Zener比与α(A2)板状纳米颗粒相似(arA = arB)时,球形颗粒形态可能转变为板状。而当主沉淀相的Zener比高于α 纳米颗粒相(arA < arB)时,颗粒可能立即呈现板状形态。
要点六:α (A2)纳米颗粒的析出对合金的力学性能有显著的影响,提高了合金的硬度和强度
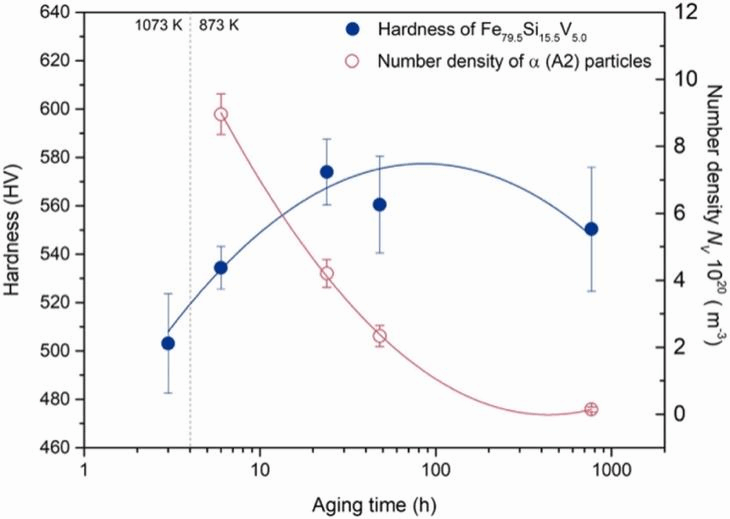
图7. 在1073 K时效3小时,随后在873 K时效6小时、24小时、48小时和768小时期间,Fe79.5Si15.5V5.0模型合金的力学性能和微结构特性的演变。维氏硬度(实心蓝色圆圈)和α(A2)板状纳米颗粒的数量密度NV(红色空心圆圈)。误差为标准差σ,根据标准误差传播方法计算。
作者表明,873 K时效后,α(A2)板状纳米颗粒的析出使得合金的硬度明显提高,并在873K/24小时后达到了约570 HV的峰值硬度,并在后续时效中(误差范围内)硬度仅略微降低。这是由于α(A2)板状纳米颗粒的析出引起了第二相强化和固溶强化的效果。第二相强化是由于α(A2)板状纳米颗粒与α1(D03)沉淀相之间的相界面阻碍了位错的滑移,从而提高了合金的抗变形能力。固溶强化是由于α(A2)板状纳米颗粒中的Fe和V的固溶使得α(A2)基体相的晶格畸变,从而提高了合金的抗剪切能力。
【文章链接】
F. Vogel*, S. Ngai, X.Y. Zhou, E. Zaiser, A.M. Manzoni, Y. Wu, W.W. Zheng, P. Zhang, G.B. Thompson, Tracking maze-like hierarchical phase separation behavior in a Fe-Si-V alloy. Journal of Alloys and Compounds, 968, 172157.
https://doi.org/10.1016/j.jallcom.2023.172157